AW Bell: Casting a collaborative international network
AW Bell was founded as a pattern-making company in 1952. These beginnings provided a solid foundation on which to build the organisation’s expertise within the casting industry. AW Bell produced its first metal casting in 1972, and under the leadership of Geoff Bell (now AW Bell Chairman), their first investment castings in 1982.
According to Dr Roger Lumley (Senior Technical Specialist, AW Bell), this, together with a drive to innovate, collaborate and deliver superior quality products and service, has seen AW Bell successfully evolve from a pattern-maker, to an automotive industry supplier, and into an advanced manufacturer of complex defence and aerospace products.
“Today, with Sam Bell at the helm as CEO, AW Bell is an AS9100D and ISO 14001 accredited supplier of premium complex, intricate metal parts, such as casting, prototyping via 3D printing, assembly technologies, and production machining. We deliver business-to-business technical solutions for advanced manufacturing in aerospace, defence, space and biomedical products,” said Dr Lumley.
Unparalleled opportunities for shared learning
AW Bell believes that those who take innovation and turn its outcomes into competitive, desirable products and services will achieve the greatest impact in the global marketplace. In many ways, it is through its collaborative efforts that AW Bell transformed its business, becoming one of Australia’s most in-demand suppliers for the defence, space and biomedical industries.
“In the past, Australian manufacturing has been known for its mass production and distribution enterprises but, today, advanced manufacturing and technology-based enterprises, including fledgling start-up companies, are becoming the new manufacturing norm,” said Dr Lumley.
“Like AW Bell, these enterprises are transitioning away from sectors such as automotive and towards manufacturing for health care, transport, mining, aerospace, space and defence. Projects within these sectors may find companies throughout the supply chain requiring assistance and collaborative efforts to deliver particular components of modern industrial research in an industry 4.0 context, specific engineering methods for manufacturing, production engineering, and more.”
“Emphasis will shift from traditional industrial engineering methods to data-driven functions and cyber-physical systems. The developing mismatch between the old and the new means that there exists an unparalleled opportunity for businesses to work together for positive outcomes and share learning opportunities,” said Dr Lumley.
Collaboration in action
AW Bell underwent a significant transformation in tandem with the downturn in Australia’s automotive industry. AW Bell invested over $4 million in research and development, and capacity building, to support its bid for the Australian Government Department of Defence’s F-35 Program.
In 2007, AW Bell was introduced to Northrop Grumman for the of supply of casting and machining services for the Electro-Optical Distributed Aperture System (EODAS)—a camera system for the F-35.
To ensure AW Bell had a point of difference, they embarked upon a collaborative research with the Commonwealth Scientific and Industrial Research Organisation (CSIRO) to develop a new, improved casting process for aluminium. Dr Lumley was seconded from the CSIRO to AW Bell for this project.
According to Dr Lumley, “The casting process produces extremely fine microstructures in the aluminium cast alloys, and as a result, we can achieve very high levels of mechanical properties. In addition to this, we used a rigorous methodology of defect identification and elimination that produced exceptionally clean metal. The combination of these features together gives us towards the theoretical maximum achievable out of the casting alloys.”
As a result of AW Bell’s collaboration with the CSRIO, their new Aluminium Billet Equivalent (ABE™) casting process was developed, helping secure the first purchase order from Northrop Grumman in 2015. Northrop Grumman endorsed the ABE™ casting process as industry-leading, achieving higher mechanical properties than that of any global competitor. Today, Northrop Grumman is AW Bell’s largest customer.
International Networks
AW Bell’s project with the CSIRO and Northrop Grumman is just one example of its collaborative business effort. The company regularly utilises international networks and collaborations with leading global research institutions, and is currently collaborating with the DMTC, Deakin University, Monash University, La Trobe University, University of New South Wales, and The Instituto de Fisica de Materiales Tandil in Argentina, on a range of diverse research programs from fundamental research, through to industry focused outcomes. AW Bell also participates in student placement programs with Pittsburg State University in Kansas, as well as La Trobe University in Melbourne.
“The collaborative philosophy of AW Bell means that we have excellent relationships with both domestic and international businesses, as well as internationally with world-renowned research providers and professional organisations,” said Dr Lumley.
Business-to-business Research and Development Activities
AW Bell is also working with BAE Systems Australia, successfully manufacturing the electronic warfare countermeasure magazine castings for the F-35. AW Bell’s work on this project makes them the only approved casting supplier of F-35 electronic warfare countermeasure magazines in the world.
In 2018, AW Bell worked together with HSV and Walkinshaw to develop a major new automotive project, taking the product from prototype using 3D printing techniques right through to sustained supply.
In 2012, AW Bell conducted a major business-to-business research and development activity with ASC. This work eventually resulted in the development of a range of strategic materials used for the Collins Class submarine sustainment. This program is ongoing as the Collins Class undergoes refitting on a periodic basis and multiple parts and an assembly are currently in production.
AW Bell is currently working on the development of a vacuum melt capability for titanium. The introduction of this industry capability to Australian shores is critical for a successful, local, modern aerospace, maritime and defence supply chain.
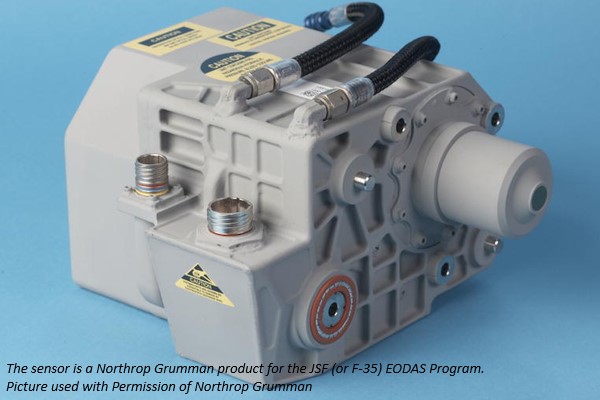