Our Projects
The Smart Think
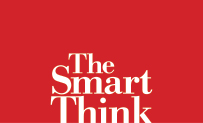
Project description and overview:
Existing composite motorcycle and motorsport crash helmets have inherent inconsistencies stemming from their manufacturing process. With these inconsistencies, manufacturers rely heavily on the physical inspection of every shell.
This project commenced when the Defence Materials Technology Centre (DMTC), Deakin University and The Smart Think (TST) developed a revolutionary composite forming technology known as ‘Double Diaphragm Deep Drawing’ (D4). The technology converts a 2-dimensional stack of composite material into a 3-dimensional object in a single step. This technology removes the need for the traditional splicing of materials for the finished products hence significantly reducing weight and producing a higher-performing composite.
TST, in conjunction with their project partners have adapted and advanced DMTC’s technology and designed a split tool version. This version is a unique cost-effective method of manufacturing that uses a combination of deep drawing and vacuum forming. The TST D4 machine is currently the world’s fastest and most advanced forming machine with an automated lay-up, cure and ejection cycle producing ballistic helmets within 15 minutes. The machine must be heavily redesigned to incorporate the split tool required to form a crash helmet and requires bespoke equipment pre-and post-processing to run effectively.
TST has performed initial validation with small scale prototype equipment, including an automated resin applicator and a robotic controlled laser cutter. This validation also included ubiquitous data collection and a longitudinal Product Lifecycle Management system that will remove the barriers to automation and online compliance checking.

EXPECTED IMPACT
- Production of the first spliceless crash helmet shell in the world.
- Production of the first Australian made crash helmet – demonstrating all seven steps across the ‘smiley curve’.
- Online compliance monitoring of entire production, including supply chain partners.
- Higher spending on R&D
- Increased collaboration with research institutions
- More staff with STEM skills
- Newer equipment
- Reshoring of crash helmet manufacturing to Australia

EXPECTED GROWTH
- Increase in revenue of $90 million over 5 years

EXPECTED JOBS
- 20 additional team members
Contributions:
Government Funds: $225,000 | Industry: $225,000 | In-Kind: $55,000