De-risking innovation through collaboration
The technology behind dragline chains—a critical component in the huge dragline excavator systems relied upon by mining companies across the globe—has not advanced in more than 40 years. As a result, the dragline chains used by the Australian mining industry are currently imported from US companies at a cost of around $100 million annually.
This is set to change.
In a project co-funded by AMGC, Cast Equipment & Chain Products (CECP) has invented and patented a new dragline chain system that will significantly increase the life expectancy of these chains, improve productivity, save on maintenance costs, and reduce downtime for the mining sector. If the project is successful, it will provide an opportunity for a local manufacturer to bring a portion of the $100 million market back to Australian shores.
According to John Kirby (Senior Investment Advisor at Burrell Stockbroking in Emerald, Queensland, in the heart of the Bowen Basin)—who has provided corporate and capital raising advice to CECP throughout the project—collaboration between the mining and manufacturing industries, research institutions, and government bodies has been vital to the success of the project.
The role of Government co-funding
“The biggest barrier to entry for this type of project is cost. There are very large pieces of machinery involved, with very high price tags that run into the millions of dollars. The more money required for a project such as this, the greater the risk. And, the greater the risk, the less likely it is that the project will commence,” said Kirby.
“So, the best way to dispel this risk is to involve a greater number of collaborators, and to ensure that there is funding behind the project. Without support from the Federal Government and its agencies, such as AMGC, who are actively encouraging collaboration, these types of projects wouldn’t happen. AMGC has been pivotal in getting this project off the ground.”
“This innovative new dragline chain might have hit the cutting room floor, if the Government had not stepped up to de-risk the project. Everyone knows that money is a show-stopper. Whether the investment is millions of dollars, or just a few hundred thousand, if it results in the expansion of Australia’s GDP by hundreds of millions of dollars, that is a fantastic result for everyone involved, from the manufacturer and their clients, right through to the Government itself,” said Kirby.
A changing culture
“Culture is definitely changing. We’ve moved from a culture where no one shared information to one where every team member is working together to achieve a common goal. On this project, we have designers, we have academia from the University of Queensland, we have hands-on specialists at the foundry level, and we have miners working together to de-risk the project.”
“The entire team has been focused on de-risking the project’s elements through collaboration. No one person necessarily has a right or wrong answer—it’s the depth of the collective opinion that de-risks everything. Multiple inputs from designers, academics and miners come together for the best possible result.”
“In mining and in manufacturing, the ‘team’ can no longer be just one person, or just one company. You simply cannot do it all alone. The wisdom of the ‘team’ is so much greater than the wisdom of the individual.”
Harmonious collaboration
“For collaboration to be successful, everyone has to work together and share information and innovations—it has to be harmonious collaboration. If you’re going to pass the ball, you have to pass it in such a way that your team member can catch it. This is my advice for anyone approaching Federal Government agencies for funding support: ensure your data is presented in a form that the agency can easily understand—or catch!”
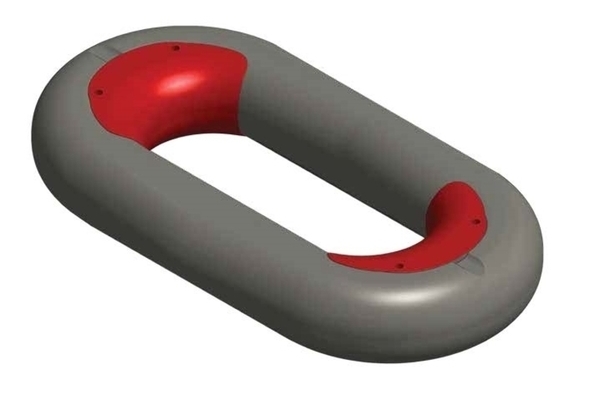